
The creation of the Zinc Alloy I-Button Gold is a story that spans multiple phases, each crucial in crafting a product that stands out both in function and design. Our journey begins with conceptualization and idea generation.
Conceptualization Phase
Idea Generation
The first step involves extensive brainstorming sessions with our design teams. These collaborative efforts focus on generating innovative ideas while considering market research and consumer needs analysis. We aim to blend creativity with practicality, ensuring that the final product meets consumer demands and sets new trends.
Initial Sketches and Prototypes
Once an idea takes shape, it moves onto initial sketches, where designers hand-draw concepts for visualization. Following this, we create detailed digital models using advanced CAD software. This transition allows us to refine designs down to the smallest detail, preparing them for the next phase.
Material Selection
Why Zinc Alloy?
Zinc alloy has been chosen for its numerous benefits in button manufacturing. It offers a robust combination of strength and malleability, making it ideal for intricate designs. Compared to other materials like plastic or brass, zinc alloy stands out for its durability and cost-effectiveness, providing a premium feel without exorbitant costs.
Gold Plating
The choice of gold plating elevates the aesthetics and durability of the I-Button. The gold layer not only adds a luxurious appearance but also enhances resistance to tarnishing and wear. Technical specifications ensure that the gold plating is just thick enough to maximize these benefits while maintaining affordability.
Design and Engineering
Detailed Design Process
From initial sketches, we venture into creating detailed 3D models. This requires close collaboration between designers and engineers, harmonizing creative vision with technical precision. Each element undergoes scrutiny to ensure that the final model is both functional and visually appealing.
Functionality Testing
Testing is integral, involving rigorous checks to ensure the button performs as intended under various conditions. Iterative testing and refining of the design are essential stages where feedback loops help improve the product based on real-world applications and stress tests.
Manufacturing Process
Casting and Molding
The casting process utilizes techniques suited for shaping zinc alloy with high precision. Our molding processes guarantee that every batch maintains consistent and precise dimensions, which is critical for the button's functionality and aesthetic appeal.
Gold Plating Techniques
The electroplating process applies the gold coating meticulously. Quality checks during this stage verify adherence to thickness standards and overall finish quality, ensuring that each button exudes excellence before proceeding to the next phase.
Quality Control Measures
Inspection Protocols
Our inspection protocols are thorough, executing step-by-step evaluations to catch any inconsistencies or defects early. Maintaining stringent standards throughout production guarantees that each product delivered matches our commitment to quality.
Failure Analysis
If defects arise, failure analysis helps identify root causes swiftly. We implement corrective actions immediately, learning from setbacks to strengthen future batches' reliability and performance.
Final Assembly and Packaging
Assembly Line Efficiency
Efficiency in the assembly line is paramount, combining automation and manual finesse to streamline the process. This hybrid approach ensures accuracy while optimizing productivity, delivering well-crafted buttons promptly.
Packaging for Protection and Presentation
A product’s perception often hinges on presentation. Therefore, we use packaging materials and methods that protect the product while enhancing its visual appeal. An excellent unboxing experience can significantly uplift customer satisfaction.
Sustainability Considerations
Eco-Friendly Materials
Commitment to sustainability means selecting recyclable and environmentally friendly materials. Our goal is to reduce environmental impact while maintaining product integrity, balancing eco-conscious decisions with practical outcomes.
Energy Efficiency
In our production facilities, energy-saving measures are implemented rigorously. Innovations aimed at reducing our carbon footprint include optimizing manufacturing processes and integrating renewable energy sources wherever possible.
Innovation and Future Trends
Technological Advancements
We constantly incorporate new technologies in our design and manufacturing processes. Predicting future trends in button design keeps us ahead of the curve, offering products that resonate with evolving consumer tastes and technological advancements.
Customer Feedback and Iteration
Consumer feedback plays a vital role in continuous improvement. Studying successful iterations based on user experiences allows us to fine-tune our products, addressing pain points, and enhancing features to meet and exceed expectations.
Behind the Scenes: Interviews and Insights
Designer’s Perspective
Interviews with lead designers reveal their creative journeys and the challenges faced during the project. Their insights highlight the dedication and innovation invested in bringing the Zinc Alloy I-Button Gold to life.
Engineer’s Insights
Engineers discuss the technical hurdles encountered and solutions developed. The interplay between design aspirations and engineering realities underscores the importance of teamwork in achieving a high-quality final product.
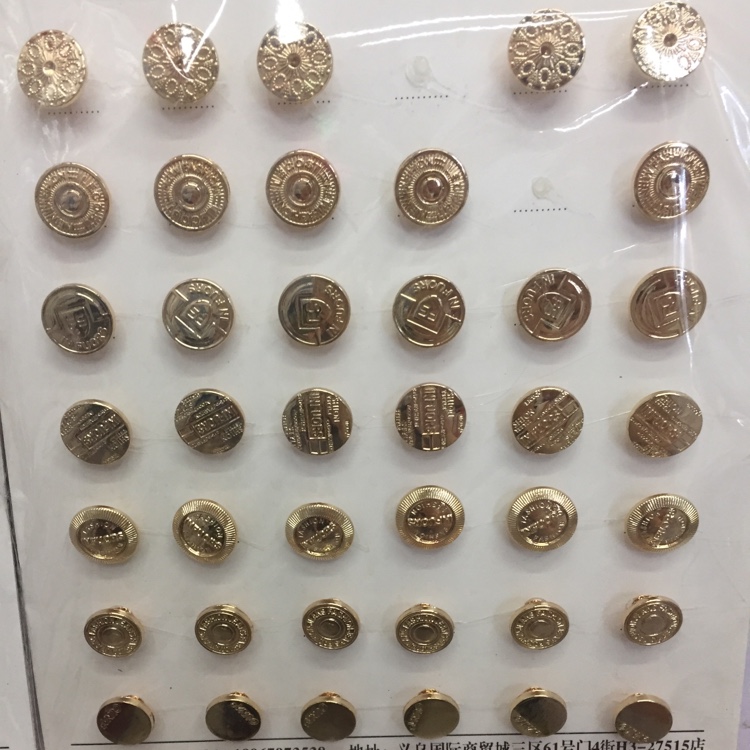
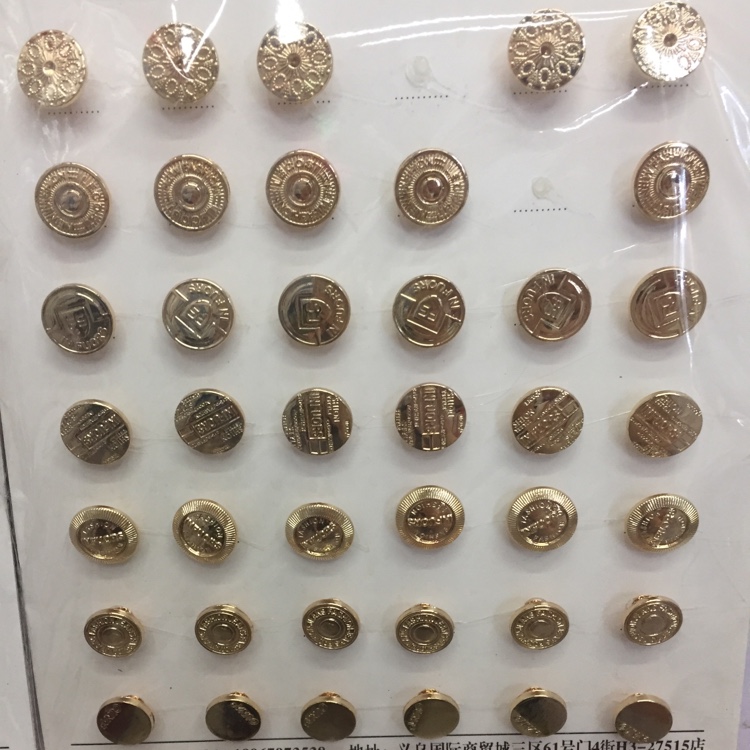